AUTHORS:Zoltan Dombovari, Jokin Munoa, Rachel Kuske and Gabor Stepan
Non-smooth torus to identify domain of attraction of stable milling processes
Non-smooth torus to identify domain of attraction of stable milling processes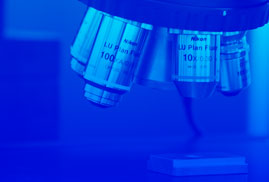
Recent technological trends tend to introduce cyber physical system (CPS, [1]) solutions in machine tools to self-sense and self-act during cutting operations. These capabilities of this envisioned enhanced machine tool [2] need to be strengthened by more accurate modelling of the combined controlled cutting process. To ensure quality and productivity requirements vibration must be attenuated. The regeneration, when the past motion of the tool excites the dynamics via the just cut surface is known since the middle of the last century published by the Pioneers in [3] and in [4]. Mathematically, the system can be represented by delay differential equations (DDEs), which generate infinite dimensional phase space. Particularly, milling is a time periodic delayed system. By this form, the asymptotic stability of the stationary cutting solution can be predicted as an important technological requirement in the industry. Unstable stationary cutting leads to the onset of growing vibration limited by a threshold effect when cutting edges, often irregularly, leave and enter the cutting state. This, generally high amplitude limiting vibration is mathematically stable. In its developed form, it is referred as chatter vibration, while the threshold effect that limits the vibration is called as fly-over by the machine tool industry. Apart from the purely nonlinear origin bistable region caused by smooth quasi-periodic solutions in milling [5], tight attraction zone can be formed around the stable stationary solution due to only the non-smooth fly-over effect. This was first experienced using time-domain solution in the motivational work in [6]. In this article island-like stability
domain (figure 1a) were presented that are enclosed by Hopf- and period doubling (PD)-kind stability boundaries. As it was shown in that paper, this was originated from the interactions of multiple modes through modulations of the main vibration frequency of the critical ’self-excited’ solution. However, in the presented particular example, this island was experienced to have tight attraction zone (figure 1b) by simulation of the corresponding piecewise linear but fly-over model. This work shows methods to predict the size of the attraction zone approximately and also to envision a general numerical description to calculate the real threshold case as a quasi-periodic solution.
MAGAZINE/CONFERENCE:ENOC 2017
June 2017